Formula Design for Hard Capsules-III
Writer: admin Time:2020-11-24 16:26 Browse:℃
5. How to select excipients for hard capsule
1) Hard capsule shell type and sizes
Currently, common capsule shells are gel shells and HMPM shells, having their own advantages and disadvantages. Formula designers can select proper excipients depending on certain properties of the medicine material. Normally speaking, gel shell is the first choice due to its low cost and stable quality. HPMC shells, although have no problem of cross-linking and are stabler, features higher cost, slower disintegration and easier variability.
Capsule size should also be considered. The common capsule size ranges from 0# to 4#. Capsules of smaller size number are actually larger and can be filled with more medicine material. In general, these capsules will be filled with the largest amount of material as they can for the largest space availability. It is also practical to fill the capsules with less material for more flexible formula design. But it should be noted that the rich space will possibly lead to some unexpected problems, such as powder leaking.
Shell size is generally determined by the preparation specification and physical and chemical properties of the drugs. In terms of preparation specification, capsules on the market normally weighs 500mg-1mg in such as wide range. Naturally, drugs in common specifications can be totally filled into these capsule shells of the limited sizes. On the other hand, excipeints which can better some properties of the compounds are added during drug processing. The poorer property the compound is of, the more excipients will be added. In this case, more good-quality excipients can be added to improve practical production and upgrade product quality, providing the drug keeps stable.
There are also some other factors to be considered during formula design. The first one is the cost. More excipients mean larger production butch, higher production difficulty, larger end preparation volume and higher storing and transporting cost. But it’s not necessary to use excessive excipients. How much excipient should be used? There is no standard answer to this question. For simply mixed powder, the proportion of active ingredients is less than 20% and they can hardly have influence on the powder. But once the API is micronized, even though the proportion is lowered to 1%, the ingredients might have effect due to their larger surface area. To better poor properties of the API and reduce dosage of excipients, granulation can be adopted. In addition, the capsule formula can be designed into a few specifications in geometric change. Besides, designers should take other changes during research and development into consideration, since condition and specification adjustment is common during production. The designers can also choose the shell whose size is exactly between the possible preparation specifications for quick specification adjustment.
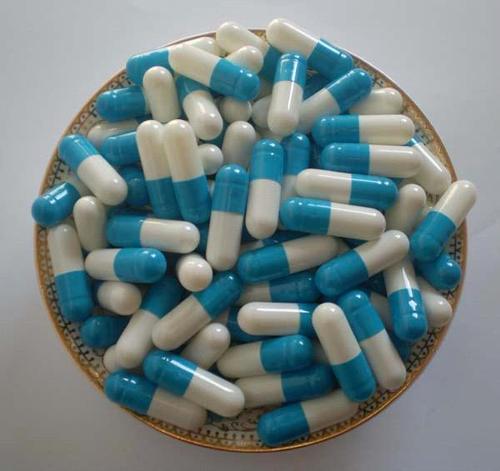
Designers can test directly if the shells suit the designed formula. However, testing on the machine directly will cause large material consumption and is not practical. The designer can also determine the filling volume depending on the tap density of the powder, if it has been measured. The real density can be the second best reference if there is no tap density.
2) Excipients for hard capsule medicine
Hard capsules basically contains excipients such as filler, disintegrant, flow aid, lubricant and surface active agent.
A. Filler
Filler is mainly used to increase volume, fluidity and compressibility of the material. Generally speaking, direct compressed filler is the most suitable excipient for capsules. Filler has the advantage of good fluidity and compressibility for smooth capsule filling. Besides, most direct compressed excipients are produced by spraying and drying. Their particles are porous to adsorb fine powder and facilitate mixing. The filler dosage is dependent on capsule shell size and other materials’ properties. The more filler is used, the more the property of the powder approaches to that of the filler. And various factors should be considered during particular dosage determination.
Besides, during filler selection, the filler’s influence on drug release should be taken into account. Some drugs are hardly soluble since their API easily reacts with excipients so that the dissolution is slowed down. For such drugs, water-soluble excipients, such as lactose and mannitol, can be better. Some water-insoluble fillers, like MCC, HPMC or starch, should be used cautiously or with other water-soluble excipients.
Among all excipients, filler is used in the largest amount. As a result, the filler have an important influence on material uniformity during filling. The size ratio of filler against the material granules can approach within 1:3 to 3:1 to avoid layering.
Some API is micronized to small size. It is prone to adhere to the equipment surface, which causes medicine content reduction, punch adhesion or unstable locking. Generally, the filler can adsorb API for their uniform mixing. But designers should pay attention to the filler’s adsorption capacity to prevent material from gathering on the equipment surface again.
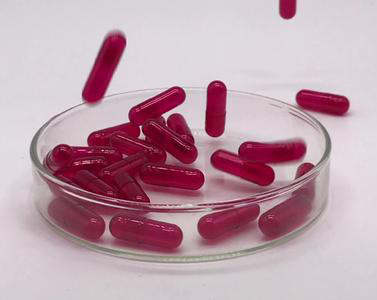
B. Disintegrant
The medicine is compressed to powder column while being filled. Although the column is not strong, some disintegrants help to improve the preparation’s quality stability and reduce influence of excipients and technical parameter change.
The powder column is highly porous, with its void fraction between 40-60%. the column contains much air and the disintegrant has just weak capillary water absorption capacity. Therefore, if the column consists of a large amount of insoluble matters, it’s difficult for the air to be exhausted or for the water to permeate into powder. Thus drug dissolution is slowed down. And if the shell is made from HPMC, the dissolution speed can be obviously slower. Volume expansion rate of the disintegrant plays an important roll in its functioning. Disintegrant used for capsules is usually twice as much as that used for tablets and accounts for 4-8% of the whole medicine. There is no doubt that disintegrant of higher volume expansion rate, such as sodium carboxymethyl starch, can perform better. However, similar to other water-insoluable filler, gelatinization of disintegrants insoluble in water can also affect medicine dissolution.
C. Flow aid and lubricant
Flow aid is usually used to better powder fluidity. The commonest flow aid should be silicon dioxide in the proportion of 0.5%. But large dosage of flow aid doesn’t mean better performance. Some material might even have weaker fluidity due to increasing dosage of flow aid.
The main function of lubricant is to reduce adhesion and friction. It can be soluble in water or not. The most used lubricant is magnesium stearate. Its proportion is usually 0.5-1% in material to be filled by metering cup. And the figure can be smaller when the material is filled by metering plate. But there is one problem of magnesium stearate, i.e., over-lubrication or over-mixing, which leads to slow dissolution. Considering that the powder is still being mixed during filling, especially on the metering plate filling machine, designers and operators should pay special attention to the phenomenon of over-lubrication.
6. Conclusion
Formula design is a systematic project. Designers should think about multiple factors and upgrade the formula by repetitive experiments. That more factors are reasonably considered at the very beginning of formula design can more improve and stabilize production and and product quality and speed up formula development.