Items |
High shear mixing |
Fluid bed granulation |
Material parameters |
Powder particle size distribution |
Wettability of the solid by the liquid |
Solid solubility & degree of swelling in adhesive |
Adhesive concentration and viscosity |
Granulation conditions |
Nozzle size & nozzle shape |
Process time |
Liquid to solid ratio & quantity of solvent |
Liquid spray rate & air pressure |
Impeller speed |
Spray droplet size |
Chopper speed |
Bed fluidity/air flow rate |
Screen mesh |
Inlet air temperature and RH |
Fill level |
Equilibrium temperature and RH in bed |
Temperature (+/-) |
/ |
Drying conditions |
Mode of drying
(air stripping, microwave, infrared) |
Inlet air temperature and RH |
Energy input |
Air flow rate |
Process time |
Process time |
Granule properties |
Screen mesh |
Particle size distribution |
Bulk density and porosity |
Moisture content |
Granule strength/friability |
As in the above table, there are four types of influence factors: material parameters, granulation conditions, drying conditions and granule properties.
Material parameters cover two aspects of raw medicine and auxiliary material, including granule size of raw medicine, wettability of raw medicine by adhesive, viscosity and thickness of adhesive… in both high shear granulation and fluid bed granulation, material parameter is a prescription factor instead of technical factor (since raw medicines are selected before production). Material factors can be ignored can it comes to technical problems.
Conditions in granulation are important in wet granulation, including size and shape and nozzle, atomizing pressure and spraying speed which will affect atomization degree of adhesive. Better atomization will provide larger contacting area of adhesive droplets and material, more uniform mixing and better effect. These parameters’ influence can be tested before loading to make sure that atomization and flowing rate of adhesive are as required. Besides, solid content and dosage of adhesive should be moderate: high solid content will make adhesive some thick and lead to agglomeration in granulator, while low solid content might not achieve expected effect.
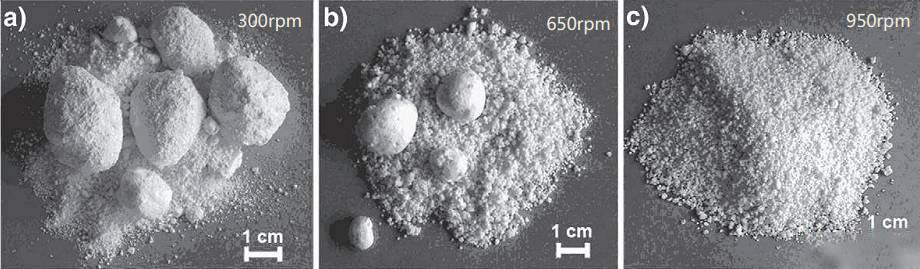
During high shear granulation, rotating speed of impeller and chopper can greatly influence granulation (e.g. granules in the above picture are made when impeller speed is 300rpm, 650rpm and 950rpm respectively). Granulation time should also be controlled. Otherwise, granulation might be incomplete or excessive. In addition, medicines loading in high shear granulation pot should be appropriate for all materials’ overturning in the pot. The loading rate is generally 30-70%. Temperature control is also very important for temperature-sensitive materials. Anyhow, the difficulty of high shear granulation is to judge its end. It is said that final granules should be blocked when squeezed and dispersed when touched. Torque or screening can also be determinants.
However, air intake speed and temperature are critical for fluid bed granulation. Low speed cannot blow up materials, while high speed will blow them to the top of filtering bags. Temperature affects drying efficiency in bed: low temperature leads to low drying efficiency and collapsed bed, while high temperature will dry spray. All in all, fluid bed granulation is a dynamic, stable and balanced process. How to keep bed in balance through nozzle, spraying speed, intake air volume and intake air temperature is the difficult of fluid bed granulation.
Wet granulation is followed by drying. Granules made by high shear granulation are dried in other equipment, such as oven (in lab) or fluid bed. They can also be dried online with microwave, infrared or air stripping. Fluid bed drying is a convenient and efficient. Its drying end can be judged according to material temperature, exhaust air temperature, loss of drying (LOD) or drying time.
Particle factors include mainly granule size distribution. Therefore, dried granules should be dry sized. And PSD, BD and angle of repose (carr index) are detected. Moisture content of dry granules is always ignored since it can be controlled during drying. However, if granules are not processed after drying but stored in intermediate station or drying chamber for several days, moisture content detection becomes necessary to check if the content is still within an acceptable limitation.
5.Conclusion
Actually, wet granulation can be affected by the above factors, as well as some other factors not referred. Except those factors, the equipment for wet granulation is also important. Different machines have their own advantages. For more fluent production, it is suggested to use machines manufactured by the same factory. Convenient installation and maintenance can also be guaranteed by doing so.