Problems and Solutions in Sugar-coated Tablet Production II
Writer: admin Time:2020-05-13 14:49 Browse:℃
7. Tablet edge is uncoated, tablets are uneven
Reason: Inappropriate dosage of coating material, thick tablet core edge, high temperature, earlier drying… Syrup and material dosage should be controlled to wet or stick to tablet cores properly. Tablets cannot be dried and heated right after syrup adding in case that high temperature and quick drying cause non-uniform syrup distribution on surface. High moisture or inappropriate pressure adjustment will produce gross tablet cores. After syrup is added, the gross edge of cores will absorb more syrup, while due to friction in coating pot, syrup will fall down and tablets edge is uncoated. Besides, that tablet edge is uncoated or tablets are uneven can also be caused by thick edge or small pot angle. When the coating pot is of a small angle, tablets will fall in high speed and collision will remove some syrup and talc on tablets.
Solution: Tablet cores should be fully dry with moisture content controlled within 2~3%. During screening, tablets can be more pressed to remove gross edge. Quantity of coating layer can be properly increased. The coating pot temperature should be controlled properly to avoid quick moisture evaporation. Dosage of syrup or powder should be adjusted to wet or stick to tablet surface uniformly. Tablets can be dried when their surface are not wet anymore in case of quick drying and even surface wrinkles. Coating pot should be adjusted to the best angle.
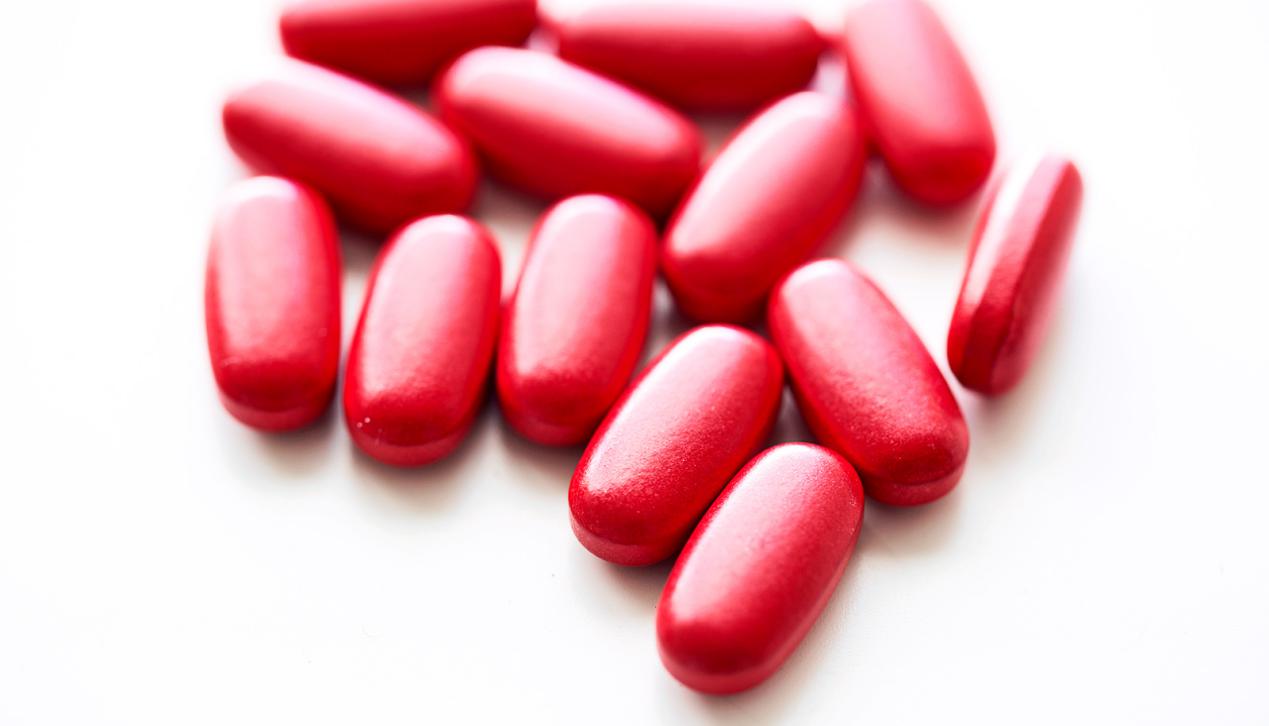
8.Tablets are not smooth
Reason: Pot wall is not smooth which is caused by high temperature syrup and drying and quick moisture evaporation. Some tablet fragments are not removed and then stick to other tablets. I this case, syrup and drying temperature and speed should be controlled to keep pot wall smooth and the pot should be cleaned timely. If necessary, dots on tablets can be cleaned and the tablets can be coated again.
Solution: After separation layer, powder coating layer cannot be processed immediately. In contrast, tablets can be rubbed for once or twice with syrup. Otherwise, powder layer cannot stick to tablets perfectly and tablets are therefore not smooth.
Coat should be thin but tablets can be coated for more times. Each layer should be dried and temperature controlled within 35-50°C. High temperature and quick drying will not give tablets chances of mutual friction so that tablets are smooth. Therefore, temperature can increase at the beginning but decline after tablets are basically coated.
Dosage of auxiliary materials can be increase gradually. When tablets are basically coated uniformly, dosage of syrup can be reduced slightly but that of talc, drastically for good transition to single sugar layer.
9.Sugar-coated tablets separate Chinese extract out
Extract and some auxiliary materials can be mixed, granulated, dried, milled and then mixed and granulated with other materials. If permitted, do not add fluid extract into adhesion on materials directly. Moisture content should be controlled during granulation in case of migration. Auxiliary coating materials should contains absorbent. Separation layer should be coated before coating. Every coat should be dried one by one. Chinese extract sugar-coated tablets can discolor when damped. Therefore, the separation layer is often coated with peach gum and gelatin.
10.White dots appear on tablets
Some tablets will generate white dots one night after coating, especially in damp or rainy days, accompanied with non-uniform coloring possibly. General solution is to add proper dosage of gelatin, syrup and talc and dry each layer. Also, the color should darken gradually but not suddenly. Moisture should be controlled before tablets are polished. End products of tablets should be stored as required.
1) Sugar crystal
During usage, syrup should be temperature preserved. To avoid sugar crystal, the concentration of syrup should be 67-70% and the using temperature cannot be less than 60°C. Low temperature will help sugar crystal to separate out. Generally, the most proper temperature for coating is 60-85°C. Besides, during production of syrup, process of heating should be controlled. Long time heating will lead to reduction of sugar, which means that sugar returns to its original condition and cannot be used in coating. Hot syrup should be used in production of color syrup since colorant mixing is a key process, too. Some mistakes might lead to unexpected results, such as white spots, stains, etc.
2) Layer-to-layer drying
White spots might be related to layer-to-layer drying. Layers of coating should be dried one by one. The next layer can be coated only after the previous layer is dried. The first layer is the most important, which can be dried in a longer time. After polishing, white spots or stains might occur during drying. That’s because of wrong drying method, high temperature of drying or wrong colorant adding method… Before color layer coating, tablets are not dried layer after layer or are affected with damp. Some tablets might be quickly dried by blowing of hot air. However, these tablets cannot be dried absolutely. Besides, non-uniform mixing of tablets during color coating will also lead to the above problem.
3) Air intake system is not clean. Some residual white foreign matters are blown in.
4) Too much syrup is added; tablets are not even; tablets rub with each other.
5) Gelatin can be added to the first to the third syrup layer. If tablets contain volatile materials, separation layer should contain more gelatin and coating temperature reduced to extend drying time of separation layer. Also, if tablets are blown for a long time and talc on their surface are blown out, sugar coating or color coating might not cover the blank and white spots occur therefore. Temperature and humidity of sugar layer and color layer should be controlled well. The former should be less than 30°C and the latter less than 55%.
6) During polishing, tablets humidity is important. Four features of tablets should be noticed, namely, hot, damp, cold and dry. Otherwise, white spots or adhesion of wax will happen. Excessive polishing will harm coating layers. Humidity of tablets during tablet airing should be controlled lower than 55% and the airing container must be dry.
11.Tablets cannot be polished
Reason: Sugar crystal is big and rough; tablets are too dry or damp; wax is damp or excessively used.
Solution: adjusting coated tablets humidity and wax dosage; controlling water content of tablets before polishing. The keys of polishing are humidity and temperature. High humidity and temperature will trouble polishing. Tablet size, together with seasons will also have influence. To avoid tablet skidding, wax should be added in batches and proper dosage. Too much dosage will cause tablet wrinkles.
1. Domestic sugar coating procedure
1) Separation layer
Screening qualified tablets and coating them with two separation layers of gelatin sugar. Feeding tablets into pot during operation and rotating the pot as some gelatin syrup is fed and mixed annually so that the syrup can be distributed on surface of tablets uniformly. Adding proper dosage of talc and continuing mixing for uniform distribution. Blowing hot air (30-50°C) to evaporate moisture in gelatin syrup and dry tablets. After drying, coating the second layer to coat tablets firmly.
2) Production of gelatin syrup for 50kg tablets
200g gelatin and 1000ml water, being heated to gelatin solution; 5kg sucrose and 2000ml water, mixing, dissolving and boiling for 3 min to produce single syrup and mixing gelatin solution and single syrup to gelatin syrup.
3) Talc coating layer
Feed warm syrup into rotary pot, mix it with tablets, wet all tablets uniformly, feed talc for its uniform distribution on tablets and then blow hot air for quick drying. This process should be repeated until all edges of tablet cores are removed. The tablet cores should be coated for 12-15 layers.
4) Production of syrup
Produce single syrup in ratio of 5kg to 2000ml of sucrose to water (for production of 50kg tablets, 20kg sucrose to 8000ml water). Sucrose should be dry granule crystals of little impurity. Syrup should be fresh and might turn to sugar after long time storage, which is not easy to be dried. Meanwhile, tablets will be rough and generate spots.
5) Sugar coating layer
The operation is basically the same with that of talc coating, but the coating material is syrup instead of talc. During operation, stop blowing after every time of syrup adding and then blow hot air after tablets surface is pretty dry. Temperature of 40°C can dry tablets surface slowly and generate fine sucrose crystal layer. This process should repeat for 9 layers.
6) Color coating layer
Coat sugar-coated tablets with medical hot melon-yellow syrup of different concentration. Syrup of light color is used first, followed by syrup of gradually darker syrup until all syrup uses up. In this process, tablets are coated for 10 times and 12g medical melon yellow should be used for every 50kg tablets.
7) Preparation of lemon yellow syrup
Syrup of dark color can be prepared at first and then be diluted by single syrup for certain concentration. Its concentration should be about 0.03%.
8) Polishing
This process should be carried out in room temperature. Stop pot rotation after the last color coating layer is to be dry and enclose and overturn the pot for slow loss of residual moisture. Then start the pot and add wax in 2/3 of needed dosage. Tablets are then rubbed and polished in rotation and then residual wax can be added until tablets are well polished.
9) Drying
Sugar-coated tablets are dried in rotary dehumidifier for 24 hours.
12.Foreign sugar coat auxiliary materials
1) Inactive ingredients of original sugar-coated tablets: 17mg sucrose, PVP-90, PEG-6000, CaCO3, talc, glycerol (85%), TiO2, yellow ferric oxide, lignite glycol wax. Among them, PEG-6000, talc and glycerol (85%) are ingredients of separation layer.
2) Inactive ingredients of Japanese original sugar-coated tablets: CaHPO3, MCC, lactose hydrate, HPC, corn starch, SiO2, calcium stearate, L-HPC, sugar, Calcium lactate hydrate, PEG, TiO2, talc and carnauba wax.
3) Inactive ingredients of original sugar-coated tablets: precipitated calcium carbonate, lactose, crystalline cellulose, talc, magnesium stearate, HPC, cellulose acetate (CA), SiO2, polyglyceryl ester, sugar, gelatin, polyvidone, gum acacia, PVA, carnauba wax, white shellac.
4) Inactive ingredients of original sugar-coated tablets: MMC, TiO2, stearic acid, calcium stearate, sucrose, talc, precipitated calcium carbonate, corn starch, lactose hydrate, white shellac, HPC, pullulan, PVP, PEG-6000, hydrated silica
Sugar-coating is a process of skill and experience, which can be operated only by well-skilled operators. Only by doing so can ingenious, beautiful, high-quality and reliable sugar-coated tablets be produced.
All in all, the most important principle for sugar coating is: small dosage, multiple layers and drying layer after layer。