Problems of Chinese herbal Medical Tablet Production II
Writer: admin Time:2021-03-08 16:14 Browse:℃
1. Sticking to the punch and die in tablet pressing
During tablet compression, a thin layer of tablets might stick on the puncher, causing roughness or scratch on the surface of tablets.
1) Mould
a. Unclean mould with grease
b. Rough inner surface of the puncher with scratch
New mould must be cleaned and disinfected before usage. The grease on the mould can be removed by wiping it repeatedly with dust-free cloth or paper and then with 75% alcohol. There is no good effect but only waste of time by wiping mould with alcohol directly. In addition, it’s not suggested to design score or patterns on the new puncher before tablet formulation to avoid drugs’ adhesion on the puncher, especially traditional Chinese medical tablets.
2) Material
a. High moisture content
It’s very common for material of traditional Chinese medical tablets to stick on the puncher because of improper moisture content. A good way to solve this problem is to find out the most proper moisture range during investigation and control moisture content during production. And the small error of rapid moisture tester doesn’t matter actually.
b. Low dosage of lubricant
c. High moisture absorption ability of material
Increase dosage of lubricants such as stearic acid, magnesium stearate and so on. If granules contain volatile oil, it’s better to add some silicon dioxide to adsorb oil and avoid adhesion on the puncher.
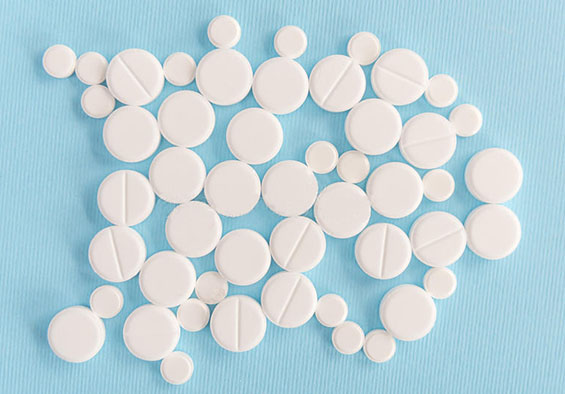
3) Environment
a. High humidity or high temperature
High-speed operation of tablet press machine will naturally increase temperature in the workshop. It’s necessary to cool the room according to requirement.
2. Tablet weight error in tablet pressing
Chinese Pharmacopoeia (2020) regulates that the weight difference for tablets below 0.30g should not exceed ±7.5% and that for tablets above 0.30g should be lower than ±5%. In investigation to 20 tablet samples, there should be no more than 2 tablets with exceeding weight difference and no tablets with weight once heavier than the limit.
1) Mould
a. Larger space of middle mould
b. Nonuniform length of punchers or nonuniform pressing position
Most traditional Chinese tablets contains crude fiber which can cause wear and tear to the mould. The mould being used should be changed after certain batches as regulated. The new mould should be checked again and again on the puncher length, pressing position and so on. Otherwise, the produced tablets will obtain excessive weight difference easily, especially the traditional Chinese medical tablets.
2) Equipment
a. Out-of-shape of some gears of the feeder
Machine mould and parts are pretty precise. They need careful storing and dismantlement. The removed parts should be placed on special mould car. Do not use the parts which are out of shape to avoid problems of tablets quality. And problems of tablet weight are always caused by improper dismantlement or store of machine parts. If possible, these parts can be stored by a specially assigned person.
b. Unbalanced feeder and turntable
c. Loose structure of machine
Train operators not only on machine operation but also on machine installation. And special operator can be assigned to operate special station to protect the machine.
d. High rotating speed and insufficient feeding
This problem is similar to the high rotating speed which leads to tablet breaking. The solution is also similar: find out the highest speed by investigation and set it.
3) Material
a. Poor fluidity, granule stratification and wide size distribution
Set granule size distribution standard, strengthen size test during granulation and sample granules every shift to reduce difference among batches.
3. Slow disintegration for tablet
Chinese Pharmacopoeia (2020) also introduces disintegration test method for traditional Chinese medical extract tablets, semi-extract tablets and powdery tablets. In the investigation, tablets are put into a test tube and each tube has a baffle. Powdery tablets should all disintegrate within 30 minutes, extract tablets and semi-extract tablets within 1 hour. If the tablet samples stick on the baffle, sample another 6pcs and repeat the test without baffle. If there is one that doesn’t disintegrate within the time, repeat the test again until they meet the requirements.
1) Material
a. Too much adhesive or lubricant
Too much adhesive or lubricant can decrease tablet disintegration speed. For instance, large dosage of magnesium stearate will slow down tablet disintegration. It’s suggested to set standard for granule size distribution and bulk density, strengthen test to material during granulation and sample material every shift to reduce difference between batches.
b. Long storing time
Granules should be compressed on the same day as they are granulated to prevent them from absorbing moisture. Besides, granules should be stored in stainless steel hopper with cover and good seal.
2) Equipment
a. High pressure of tablet press machine
Regulate and set equipment speed and pressure limit depending on the technical investigation and stick the regulation on operation panel to remind the operators.
4. Rough tablet or tablet pit after film coating
Tablet pit refers to the roughness and pockmarks on the surface of tablets.
1) Material
a. Granule falling
Some tablets will lose granules during coating. The uncoated tablets are smooth but become pitted after coating. One cause is nonuniform mixing of dry and wet granules. Dry granules are poorly viscous. Although they can be compressed to tablets, they will fall down when they are heated and coated. The granule moisture content should be controlled during granulation and the mixing time can be moderately extended.
5. Variegated tablets
Tablet variegation is the uneven color of tablets which looks like watery patterns.
1) Material
a. Caused by coating, hard granules, uneven mixing or moisture migration
Control moisture content during granulation, extend mixing time moderately and increase heating temperature properly to preheat tablets and coat them quickly.