Installation, Operation and Cleaning of V-blender
Writer: admin Time:2020-09-11 17:50 Browse:℃
High-efficiency V-blender is the mixing equipment for powder and granule, with wide application in pharmaceutical industry, chemical industry, foodstuff, plastics, cosmetics, ceramics and metallurgy.
Since some advantages of similar foreign machines are introduced, our machine is optimized. Since its two cylinders are of different length, the V-blender is actually asymmetric. While the machine is rotating, material obtains different potential energy for separation and combination and thus form expansion mixing axially. Besides, material at different level also obtains different potential energy, which also causes horizontal convection mixing. The both mixing motions continue for uniform and random mixing of material.
V-blender adopts gravity mixing for low pressure on material and high mixing uniformity. Besides, it is made of stainless steel and polished internally and externally to save energy and improve efficiency.
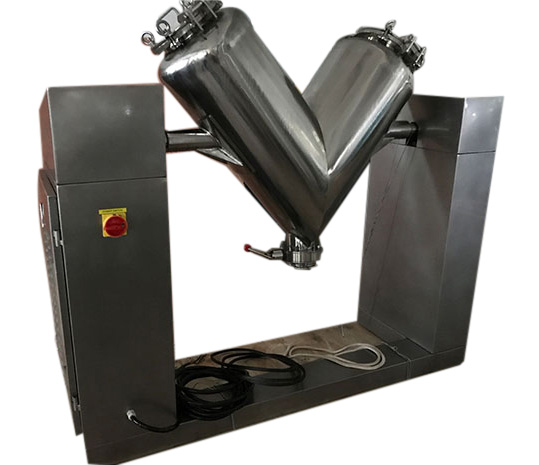
Material can be fed manually or by vacuum and discharged with a butterfly valve. Therefore, the operation can be dust-free and cleaning can be convenient for formula changing. All in all, the above advantages make V-blender an ideal mixing equipment of new generation.
1. Installation, operation and maintenance
1) Installation
A. The machine is out of factory without splitting. Professional installation personnel can install the machine and keep it level;
B. Check whether reducer is lubricated;
C. Professional electricians can connect the machine with power supply according to electrical diagram.
2) Vacuum feeding (option)
A. Tighten the two glands, connect material feeding pipe with feeding connector and vacuuming connector with vacuum connector, and close material feeding valve;
B. Insert material feeding pipe into prepared material and vacuum;
C. After enough material is fed, switch off vacuum pump, dismantle material feeding pipe and vacuuming pipe and tighten connector cover.
3) Material feeding
A. Open the large material feeding cover, switch off material feeding valve and feed material;
B. Tighten the material feeding cover.
4) Electrical control
A. Switch on the power supply, press “Start” button to run the motor and start operation of mixing machine;
B. Press “Stop” to stop operation of machine;
C. Press “Jogging” to adjust material feeding position.
5) Material discharging
A. After mixing, stop the machine first, press “Jogging” and adjust the bucket to the right position for material discharging;
B. After the machine stably stops, open the material discharging valve and discharge mixed material into a prepared container.
6) Notes
A. While starting the machine, notice the bucket motion route, clear away all personnel or matters and make sure that no personnel or mobile objects can be close to the route;
B. Before using, test the machine without material. And before test, check all connector parts, lubricating oil in reducer and completeness of electrical appliance and then switch on and test;
C. Before operation, lubricate all parts necessary and test the machine without material to check fastening parts, electrical devices and normal operation. Debug and test again for any abnormality;
D. Turn the material feeding port upwards, open material feeding cover and feed material. It should be noted that material feeding amount cannot exceed the specified volume. Then close the cover and start the machine. Stop it and have a check for any abnormality;
E. Before the machine stops, operators should not be close to and operate the machine;
F. Operators should not be close to and operate the machine during machine jogging;
G. After shift or product change, clean the hopper thoroughly.
7) Maintenance
A. During working of new machine, the reducer should be lubricated again in two weeks and lubrication be carried out by professional fitter: open the side door, open the drain plug and screw it after filling oil. Feed 30# machinery oil. And maintain the motor and reducer according to the machine manual;
B. The grease for upper bearings of machine frame should be changed every 5000 hours and the lubrication can be done only by professional personnel;
C. During production, pay attention to loose parts, abnormal noise and check the cause and clear errors by professional fitters and electricians for any abnormality;
D. All maintenance operations should be done after the machine is powered off.
2. Cleaning of V blender
1) Cleaning conditions and frequency: cleaning once while changing products, formula or batch of the same product;
2) Cleaning tools: barrel and rag;
3) Detergent and formula: soap being diluted (proportion between soap and water is 1:10)
4) Scrub the machine with dish soap;
5) Fill drinking water into V-tank (purified water for purifying zone) and run the machine for 5 minutes to wash thoroughly. Repeat this operation for three times to no dish soap residue;
6) Disinfecting conditions and frequency: disinfecting once every Saturday, after maintenance and for any quality problem;
7) Disinfecting parts: inner and outer material feeding port, inner wall, inner material feeding port cover and tools contacting material;
8) Disinfecting tools: barrel and rag;
9) Disinfectant: 75% alcohol, 3% hydrogen peroxide;
10) Disinfecting way: dip the rug or sponge glass brush with 75% alcohol or 3% hydrogen peroxide.