1.Introduction
HLSG series high efficiency wet granulating machine is our granulator of new generation. It can mix, moisture and granulate. It features high efficiency, good performance and conformance to GMP requirements.
As an integration of photo, electrical and pneumatic, the machine applies PLC for control, HMI and touch screen for display and operation, frequency control of speed and photoelectric detection and some other leading technologies. Besides, we also innovate adhesive feeding system to feed adhesive by dropping or some other ways, automatic safeguarding devices, pot jacket cooling system and temperature control system. As a result, this machine features perfect functions, high automation, less adhesive consumption, short granulation time and good product quality. It can mix and granulate powdery or paste materials into firm granule products of uniform size and high porosity rate. Thus the machine can be used in many fields, including pharmacy, foodstuff, chemicals and metallurgy. One special application of machine is to granulate traditional Chinese medical extract or powder, which offers a new way to transform traditional Chinese medical herb to patent medicine.
2.Performance and features
1)The machine controls temperature, operation time, speed and formula through PLC and displays them on HMI for both high automation and convenient operation;
2)A pair of V-cutter is additionally installed in cutting system on the basis of traditional straight-handle cutter. Therefore, the cutter can not only pare, but also cut vertically to shorten granulation time. Exclusive mixing paddle can scratch away material adhering to container wall, reduce material sediment at the bottom or inner wall of container, avoid granules’ impact to inner wall, improve granulation and porosity rate and decrease fine powder to under 8%.
3)The jacketed pot can cool material according to practical requirements. The temperature is controlled by PLC with an error within 2°C.
4)The machine is equipped with a set of dropping device to feed adhesive in different ways according to material properties. Adhesive can be dropped into material or mixed with material directly. In this case, it can be saved by about 20% but materials can still be granulated well.
5)Safety protecting devices are reliable. Only password can start the machine when hopper cover is even opened. By this means, operators and machines can be protected. A port for vacuum feeding is set on the hopper cover. Additional dust collecting device and adhesive feeding device enable the machine to granulate in dust-free condition;
6)The rotating shafts of cutter and mixing paddle are sealed by both skeleton seal ring and spiral aeration. This method solves a big problem of frequent fault of shaft seal. In addition, the shafts are removable or dismantlable for convenient maintenance;
7)Mixing and granulation are finished continuously, which improves production efficiency by 4-5 times. The final products are firm granules of uniform size and high porosity rate. This machine can even mix and granulate traditional Chinese medical powder or extract whose proportions of ingredients and excipients are discrepant.
3.Working principle
This machine adopts jacketed pot as hopper and applies mixing paddle and cutter to provide power. During operation, the mixing paddle mixes material in set speed. Then a material feeding device feeds adhesive, which is also mixed with material. High-speed rotary cutter can cut the mixture to granules as required. At last, granules are discharged out. Rotating speed of mixing paddle and cutter can be controlled in order to produce granules of variable size.
4.Main structures
1)Machine body
This part is welded from angle iron and plate steel and its surface is made up by stainless steel. It mainly functions to support other parts, which are installed inside it, including mixing motor, mixing reducer and pneumatic components which drives the pot cover to move upwards and downwards or rotate forwards and backwards.
2)Mixing part and jacketed pot
The power for mixing comes from a motor and the mixing shaft is exactly the output shaft of reducer. The mixing paddle is fixed on mixing shaft. Under machine table is motor and reducer, while on it is the jacketed pot, between which a set of removable or sealed components is installed.
3)Cutting structure
Cutting structure consists of a motor and the cutting shaft connected with motor shaft. Cutting knife rotates at high speed in the pot and cuts material to granules continuously. An enclosed structure is installed between cutting shaft and motor base.
4)Pot cover
Pot cover is made of stainless steel. It look like a cap of pressure vessel. Under the cover is a T-type silicone seal ring. An upright can drop down the pot cover to seal it with pot. Pot cover also has holes for observance, liquid feeding and air exhaust.
5)Material discharging gate
The material discharging gate is installed on a anti-rotation cylinder. When the cylinder moves forward, clean air can be jetted to the discharging gate and remove dust. As a result, the gate is closed. On the other hand, cylinder’s moving backward will open the material gate. Granules can thus be discharged under pushing of paddles.
6)Automatic mixing paddle lifting device
Our wet granulators is equipped with an automatic mixing paddle lifting device (HLSG-100 or smaller machines are not equipped). This device can lift mixing paddle through cylinder for thorough cleaning granulation pot, observance on parts hidden by mixing paddle, no dead corners and no cross contamination.
5.Technical parameters
Model |
HLSG-300 |
Hopper volume |
300L |
Material feeding |
30-120Kg/batch |
Operation time |
Mixing: about 5min
Granulation: 3-15min |
Granule size |
About Φ0.14-Φ2.5mm |
Mixing motor |
18.5KW, 6 poles |
Rotating speed of mixing paddle (frequency control of speed) |
30-220rpm |
Granulating motor |
5.5KW, 2 poles |
Rotating speed of granulating paddle (frequency control of speed) |
50-3000rpm |
Compressed air |
0.5m3, 0.7MPa |
Connector for cooling water |
Φ10mm |
Connector for compressed air |
Φ10mm |
Height of product discharging port |
985mm |
Machine dimensions |
2420*1060*2150mm |
Machine weight |
About 1600Kg |
5.Technical parameters
No. |
Name |
Model and Spec. |
Qty |
Brand |
1 |
Frequency converter |
VFD185B43A |
1 |
DELTA |
2 |
Frequency converter |
VFD055M43A |
1 |
DELTA |
3 |
Touch screen (color) |
SMART 700 IE |
1 |
SIEMENS |
4 |
PLC |
ISR30 -0AA0 |
1 |
SIEMENS |
5 |
Master switch with lock |
ZB2-BG2C |
1 |
SCHNEIDER |
6 |
Circuit breaker |
C32N3C/63/50/25 |
1 for each model |
SCHNEIDER |
7 |
Single-pole circuit breaker |
C32N1C/10 |
1 |
SCHNEIDER |
8 |
Switching power supply |
S-50-24 |
1 |
DELTA |
9 |
Small relay |
RXM2LB2P7 |
4 |
SCHNEIDER |
10 |
Circuit breaker |
LC1E65M5N |
1 |
SCHNEIDER |
11 |
E-stop switch |
ZB2B54C |
1 |
SCHNEIDER |
12 |
Temperature controller |
SW-C4 |
1 |
|
13 |
Thermocouple |
K type |
1 |
|
14 |
Motor |
Y180L-6, 18.5KW |
1 |
LICHAO |
15 |
Motor |
Y112M-2, 0.55KW |
1 |
LICHAO |
16 |
Electromagnetic valve |
4V-210-10 |
1 |
AIRTAC |
17 |
Electric connect voltmeter |
1.6MPA |
1 |
|
18 |
Electromagnetic valve |
4V230C-08 |
1 |
AIRTAC |
19 |
Buzzer |
AC220V 0.25W |
1 |
|
20 |
Electromagnetic valve |
4V210-08 |
1 |
AIRTAC |
SZ series Wet Milling Machine
1. Introduction
SZ series wet milling machine is applicable in pharmaceutical, food, fine chemical industries. It conforms to GMP and is completely made of stainless steel.
2. Working principle
Raw material is firstly fed into a conical chamber of the wet milling machine. Rotating knife will swirl material and throw it to the screen due to centrifugal force. At the same time, high-speed rotating knife generate shearing force with the screen, which grinds material to small granules and pushes them to pass through the screen. The granule size is determined by screen mesh, distance between rotating knife and screen, as well as rotating speed.
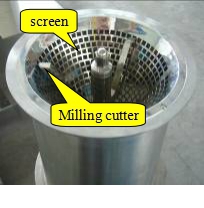
Granules are discharged in two ways after wet milling:
A. Direct connecting: Discharging port of wet milling machine is connected with input port of fluid-bet granulating and drying machine through conveying pipe. A directly connected discharging device can be installed under the wet milling machine. Another end of the device is connected with a conveying pipe. Under the force of negative pressure in fluid-bed granulating and drying machine, wet granules are sucked into and dried in fluid bed. Its advantage lies in that material is always in an enclosed system from wet granulation to drying.
B. Direct dropping: Granules after wet milling drop into a storing container or a hopper of fluid-bed granulator and drier.
3. Technical parameters
Model |
SZ-500 |
Motor power |
4KW |
Output |
80-300Kg/h |
Screen size |
3*3-6*6mm |
Rotating speed |
Up to 1600rpm through frequency control of speed |
Rotating speed of cutter |
200-1600rpm |
Screen shape |
Square: applicable for wet milling |
4. Electrical components
No. |
Name |
Spec. and model |
Material |
Qty |
Brand |
1 |
Main machine |
SZ-500 |
SS304 |
1 |
By ourselves |
2 |
Frequency converter |
VFD040M43A |
|
1 |
DELTA |
3 |
Motor |
Y90L-3.7KW |
|
1 |
LICHAO |
4 |
Electrical appliance |
/ |
|
1 |
SCHNEIDER |
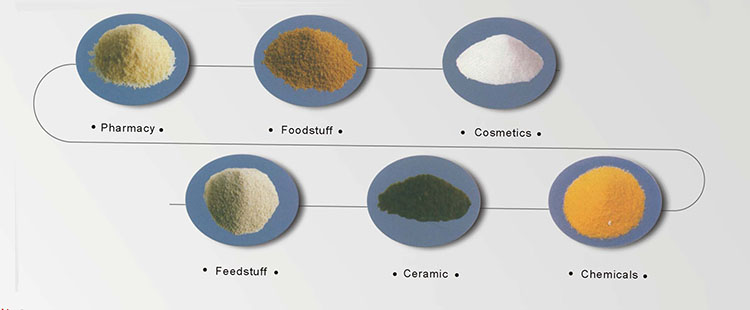
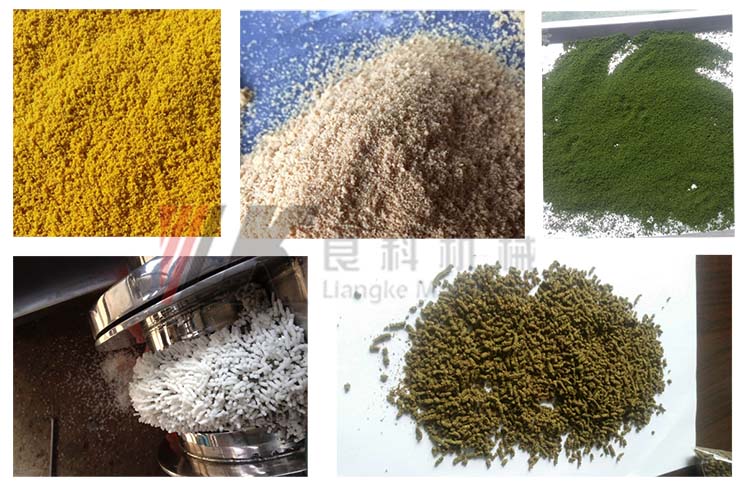
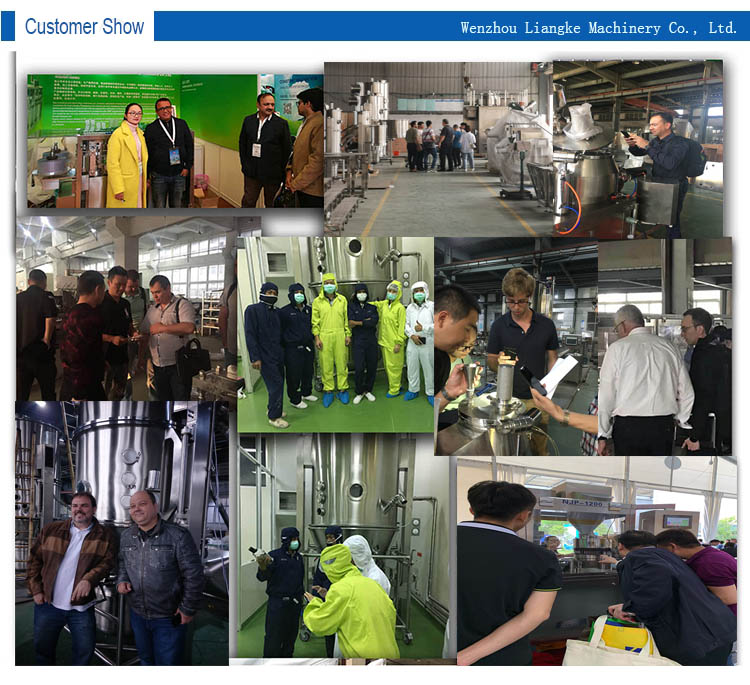
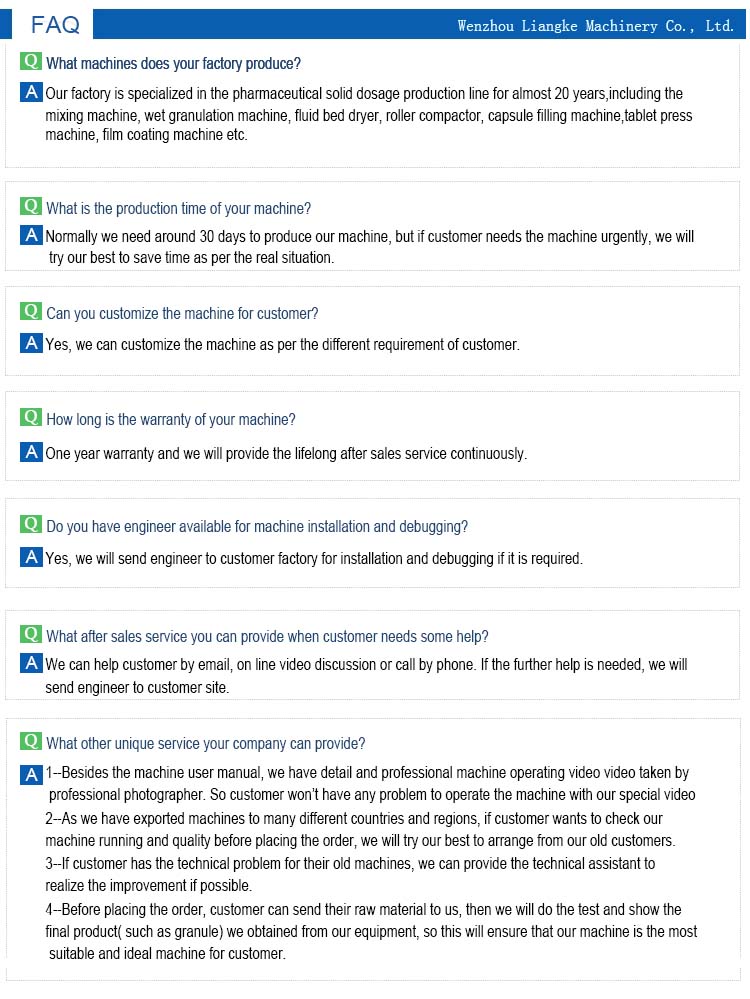
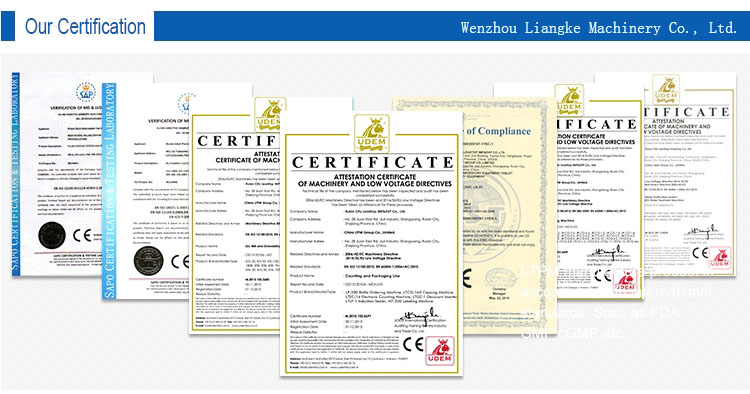